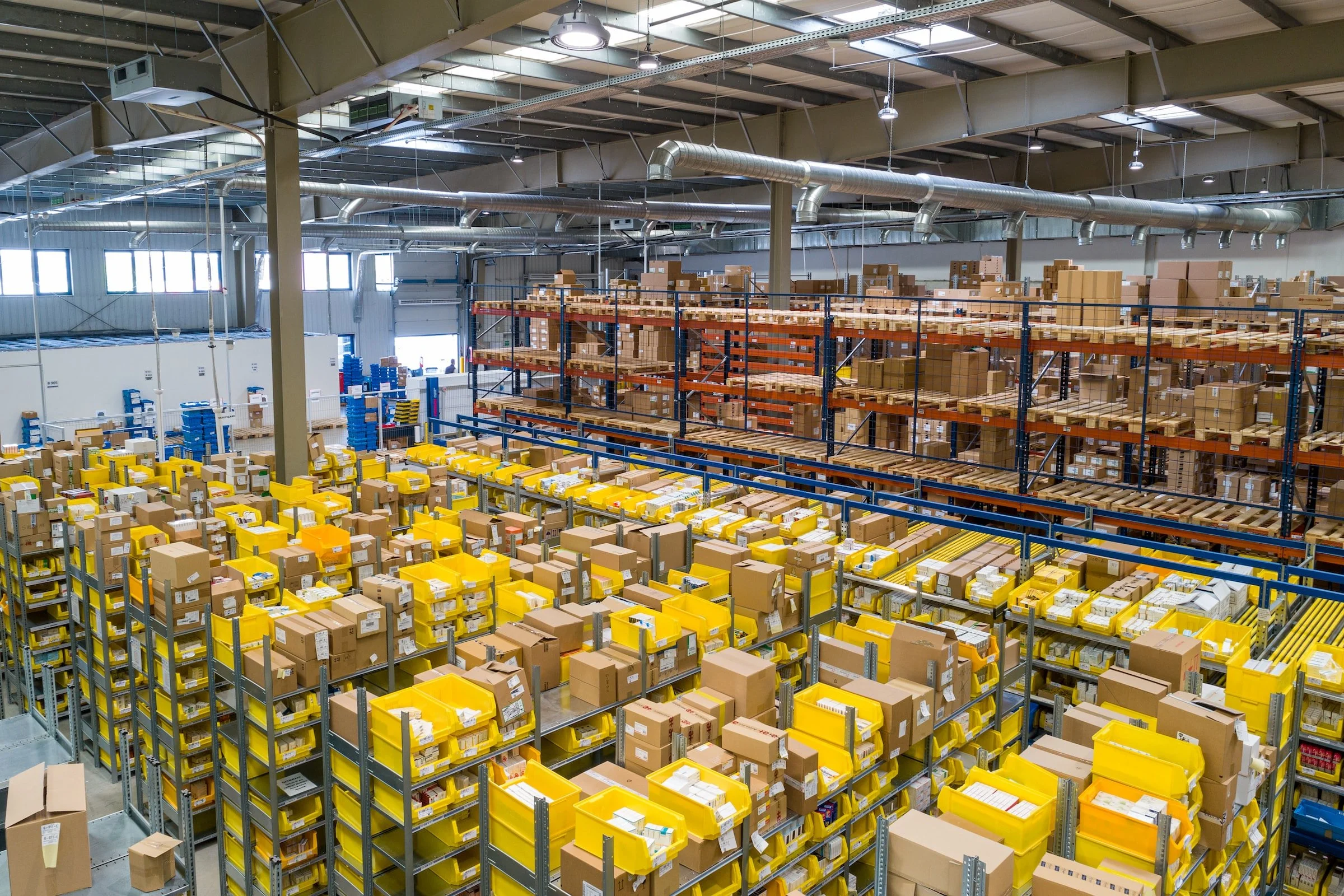
CVS Warehouse Optimization
Optimizing for Throughput
The purpose of this project was to find cost-efficient ways to minimize throughput variation at the loading dock of CVS Pharmacy’s Indianapolis Distribution Centre (DC).
Summary of Methods:
The team employed a number of methods in order to address this issue. Firstly, multiple site visits were undertaken to better understand the process and to identify the key contributors to throughput variation. In addition to observations, stakeholder interviews provided further insight into the variation on the loading dock. A simulation was created in order to emulate the maximum achievable throughput of the improved loading process and a cost analysis was carried out to help leadership visualize the feasibility of the possible solutions. The 5S methodology was also employed to systemically deploy recommendations. Lastly, an ergonomic assessment was conducted to understand the risks and benefits of current processes and feasible solutions on the loading dock.
Summary of Recommendations:
Based on interviews, simulation results, and feasibility study, a loading dock re-design that incorporates the use of a recirculation conveyor table, in adherence to 5S standards, was recommended. Our task analysis and ergonomic assessment also led to the recommendation of manual hand-held wrappers. The CVS team also received a list of future recommendations including automatic pallet wrappers and Warehouse Work In Progress monitoring screens.
Sponsors & Team
Our project was sponsored by Purdue University as a part of the Industrial Engineering Senior Design course. A team of five Industrial Engineers executed the project:
Austin Shaffer
Mohd Iramul Hoque
Natalie Geraci
Sofia Vallet
Varun Patil
Discovery
Given that throughput was the key driving metric for the warehouse, our team set up to identify the factors that contribute to it:
Site Visits revealed the process flow for identifying the correct tote to ship by loading it onto the truck as seen in Fig 1.1
Our team immediately identified two process steps (#8 & #9 in Fig 1.1) that were contributing to re-work and variable delays
We determined that a time study would be essential to quantify the bottlenecks that were observed and use the data to create a simulation that replicates the current throughput
Given the labor-intensive processes of palletizing and loading, we interviewed relevant associates to get a better understanding of the nuances in the process and found that they validated our initial assumptions of repetitive tasks and called out tasks that caused physical strain
Figure 1.1 Tote Shipping Workflow
Methods
Data Analysis
Our team requested DC routing matrices and yearly throughput data from the warehouse to better understand the variation on the loading docks. A large part of the analysis included sorting the data in a meaningful manner to help the team realize the weekly and monthly fluctuations, which helped identify routes and days of heavy traffic. Additionally, the provided data was used to generate values for use in a simulation to model the DC’s loading dock. It was noted that variables such as seasonality could play a large role in the throughput variation throughout the year.
Figure 2.3 Simulation Flows
Figure 2.2 Throughput Scorecard
Simulation
Two simulations were created in a simulation software called Arena by Rockwell Automation. The first simulation was created in order to replicate the DC’s current throughput and the second was created to emulate the scenario after the suggested improvements were implemented.
As seen in Figure 2.3, the main purpose of implementing the solutions was to eliminate the re-stacking process which has been identified as the largest contributor to the throughput variation seen in the distribution center.
The parcels are created at a rate of 1 entity per second using a random exponential distribution, which is the rate at which CVS runs its barcode sortation system (60% of capacity). The simulation models the loading process from the point at which parcels are sorted to 1 of 22 conveyors that merge piecewise to form approximately 12 lanes. This assignment is done using a random round-robin setting with a parcel having an equal probability of going to one of the 12 lanes. After this parcels are batched into pallets of 48 after which it undergoes 2 processes, wrapping, and loading which have associated processing times based on a triangular distribution.
The key difference between the current process and the ideal process is the elimination of re-stacking as stated earlier. In the current process, there is an additional decision module that checks to see the weight attribute assigned to each pallet when it is routed to a conveyor and if it exceeds 450, an additional process of re-stacking is incurred with an associated processing time which is once again created using a triangular distribution. Each parcel is assigned a weight between 2 and 16 (in kgs).
Finally, after wrapping and loading the entity exits the system and the statistics are recorded.
Figure 2.1 Routing Matrix
Figure 2.4 Current State Simulation
Figure 2.5 Ideal State Simulation
5S Methodology
Based on observations and stakeholder interviews, adjustments to the design of the loading dock using an implementation of 5S principles contributed to the overall recommendations to the CVS distribution center. The 5S ideology has 5 systematic steps to organize workspaces, which include “sort”, “set in order”, “shine”, “standardize”, and “sustain” (Chapman, 2005). Each step builds on its predecessor, and multiple iterations of 5S create a cycle that allows for continuous improvement. The following outlines the recommended way to implement 5S:
Sort: Gather items cluttering the immediate work area and take inventory of needed items. For items whose need is questionable, place a red tag or marker on them in a central area. These red tag items should be discarded in a period of about 2 weeks if they remain unused.
Set in Order: After sorting items, it is useful to organize them. This can include designating clear areas for items. It can be helpful to indicate areas with colored taped-off areas, containers, paint, etc.
Shine: Keeping the work area clean is an important component of success in the 5S process. Assigning housekeeping tasks to specific areas will help define cleanliness standards.
Standardize: The implementation of the 5S process should be maintained by establishing standard procedures and providing necessary organization resources. Involve employees in discussions for establishing the standards, and re-visit procedures regularly to ensure continuation and improvement. Provide necessary resources such as brooms, rags, labels, paint, etc to maintain the workspace organization and cleanliness.
Sustain: To ensure the 5S system is maintained, continue to keep employees involved and trained in 5S processes. (Chapman, 2005)
Figure 2.6 5S Methodology
Task Analysis & Ergonomic Assessment
To understand a critical part of the overall process a hierarchical task analysis was performed (Figure 2.7) to determine how a pallet was built. First, the palletizer, someone who loads a pallet, stages a pallet in the designated area. Next, he or she will take the parcel, box or tote, off of the conveyor belt and then put it onto the pallet he or she had staged in the previous step. The following step occurs most of the time when stacking corrugated boxes but can happen occasionally with totes as well. The operator will have to restack the pallet. This occurs when a heavier parcel comes down the conveyor after lighter parcels have been placed on the pallet. They will have to take off the lighter parcel and set it on the ground. Next, they will take the heavier parcel and put it onto the pallet and only after completing this task can they pick up the lighter parcel off of the ground and place it back onto the pallet. Once the pallet is fully built it is time for the last step which is to wrap the pallets in plastic wrap.
In order to determine the physical risk the workers were in while performing their various duties a Rapid Upper Limb Assessment (RULA) was performed. The primary analysis was looking at building a pallet. In order to perform these analyses images were taken of an individual performing the palletizing task or observed while performing the task.
Figure 2.7 Hierarchical Task Analysis of Loading Process
Figure 2.8 Rula Assessment Sample
Results & Recommendations
Simulation
The total pallet throughput observed in the current process based on this simulation was 1002 pallets which translates to roughly 48,000 parcels per day or 16 hour shift. Multiplying this number by five yields a weekly parcel throughput of 240,000 which is almost identical to the weekly throughput numbers provided to the team earlier in the semester. As for the ideal process, the final pallet throughput recorded was 1122 pallets which is roughly 54,000 parcels per day, meaning 270,000 parcels per week. This translates to about a 12% increase in total throughput through the implementation of the recommended improvements of the recirculation conveyor table and the manual, hand-held pallet wrappers suggested in this report.
Loading Dock Recommendations
Based on the 5S methodology and observations of the current loading dock, recommendations for 5S implementation, as well as loading dock design improvements and additions have been suggested for application to the CVS loading dock. The following 5S implementation has been recommended:
CVS 5S Strategy Recommendations:
1. Sort - Take inventory of equipment such as material handlers and forklifts. Gather loose items such as pallets, miscellaneous items that do not belong on the dock, debris, etc. Red tag the items that are expected to no longer be needed. Place red tag items in a central area for access; after a period of 2 weeks, discard the items that still remain unused.
2. Set In Order - Distribute material handlers based on need throughout the lanes, assign areas for items that need to remain on the dock, and move damaged/restock items to the assigned areas.
3. Shine - Clean the work area daily and incorporate housekeeping tasks into shift transitions for increased associate ownership of the area. Housekeeping tasks can include sweeping, removing unneeded items, and overall tidying.
4. Standardize - Include employees in a discussion to establish standards for the work area. Establish the expected tasks for housekeeping before shift transitions and end of the day. Bring loading dock employees into the discussion and establishment of standards; keeping them engaged is important if the implementation of 5S is going to be successful. The associates on the loading dock may also bring good ideas for the new process since they are familiar with the environment and day-to-day tasks.
5. Sustain - Maintain changes with training and communication for the new process. Iterations of this process allow for continuous improvement of the process and established standards. Keeping the conversation going during regular meetings can be helpful too. Try to incorporate 5S into the conversation for updates during weekly or bi-weekly meetings.
Recirculation Conveyor Recommendations
Based on the observations and stakeholder interviews, as well as 5S ideology, a conveyor table was recommended for implementation at the base of the conveyor belts. The current frequency of pallet restacking is a driver in the recommendation, but safety and ergonomics are also contributing factors. The conveyor will allow associates to easily sort packages by weight by quickly moving them to the side on the additional recirculation table when it comes down the lane. The implementation of a conveyor table will also reduce the presence of clutter currently caused by restacking and staging of products based on weight. Overall, the implementation of a conveyor table would efficiently streamline the palletizing process.
Layout Design Recommendations
The new design recommendations feature color-coded designated areas for items needed on the loading dock. The specific recommended areas include an area for forgotten/restock items, an area for damaged items, and an area for small cart storage. In addition to these designated areas, the pallets should be kept orderly as possible by using only what is needed in front of the conveyor lines. A recirculation conveyor table is also added to the recommendations for the new layout. A designated area for material movers and forklifts is not shown in the layout but is suggested for implementation to reduce time wasted looking for them during shift transitions, as well as the clutter caused by the uneven distribution of material handlers through the lanes. In the image below, a detailed close-up of the recommended improvement is shown for the loading dock.
In the image above, the loading dock is shown with suggested areas for items. The “Recirculation Roller Table” is located one-third of the distance further back from the front of the end conveyor. This location was chosen to allow for associates to still be able to work on the side of the conveyor without disrupting the way they normally work. This location will also allow the associated to easily shift items to the recirculation conveyor almost instantly without having to make any wasteful transitions.
The areas for the forgotten/restock items as shown in the image above were chosen to be under the overhead conveyor declines. These areas seemed to have pallets used for items that did not belong in the loading dock area, but there was a lack of organization and emphasis on the use of the space. As part of the implementation of 5S, these areas should be cleaned and organized, and these areas should also include clear signage to indicate the space’s use. In addition to the initial cleaning and organization, there should be tasks dedicated to ensuring the minimization of items in these locations. Shifting idle workers to address restocking and damaged items can help minimize idle workers while also minimizing the clutter on the loading dock.
The cart storage is shown towards the back of the image, and these areas are not featured on every lane as shown in both figure 3.3 and figure 3.4. Based on the understanding of the use of the small carts, they are only used for city stores where associates have to wheel products through the front doors of the store due to space limitations. Because these carts are not constantly in use, they should be consolidated in an area that will minimize obstacles to associates on the loading docks. A detailed image of the layout can be found in appendix A with dimensions for locations on the loading dock based on measurements during site visits.
RULA Improvement
The RULA assessment is scaled from 1 through 7, with 1 being the best and 7 being the worst score a task can obtain. As shown by the initial RULA Assessment figure 3.5 the resulting score of loading pallets was 7, meaning that the task needed to be investigated immediately and changed right away. By introducing the recirculation table, it could be assumed that pallet stacking task no longer needed the restacking aspect of the task analysis which was a poor ergonomic practice. The largest effects of the assessment can be seen on several steps which include: Lower Arm Position Assessment (2 to 1), Wrist Position Assessment (3 to 1), Neck Position Assessment (4 to 1), and Trunk Position Assessment (4 to 1). The final results can be seen below in figure 3.6 for a comparison of the entire assessment.
Manual Wrappers
The CVS team agreed to with our recommendation of manual wrappers to improve the wrapping effectiveness and worker ergonomics. The average operator could wrap the pallet with precise tightness and speed, previously only noticed in time studies of the most experienced operators when they used their hands. The manual wrapper allowed the user to have an ergonomic hand hold as seen below in figure 4.7, instead of directly holding onto the center tube of the plastic wrap which caused awkward hand and wrist positioning.
Cost Analysis
The layout redesign changes, along with the suggested purchase of pallet wrappers provided the aforementioned throughput and ergonomic improvements. It was imperative to analyze whether these recommendations were economically sound. As such, a cost estimate for the initial investments for the purchase and installation of the recirculation tables and pallet wrappers was made per conveyor belt in the loading dock. In addition, the maintenance cost of $50 (adjusted to 2018 dollars) per conveyor table was also factored into the calculations.
As for the returns, the savings rate was calculated using the following equation:
Savings = (Original Throughput + Hours Per Day) x Operational Days per Year x Hourly Wage Rate
Saving calculations account for an 18% standard industry depreciation rate and a 2.5% inflation rate, hence all amounts have been presented in 2018 dollars.
Figure 3.1 Recirculation conveyor table
Figure 3.2 Existing Loading Dock Layout
Figure 3.3 Updated Dock Layout
Figure 3.4 Dock Layout Legend
Figure 3.5 Initial RULA Assessment
Figure 3.6 Final RULA Assessment
Figure 3.7 Hand Wrapper Tool
Figure 3.8 Cost Analysis
Conclusion
The team has worked towards recommendations that are easy to implement and would provide a significant boost to the distribution centers’ throughput. The cost-effective solutions help streamline the stacking process and improve worker morale through the addition of cost-effective and ergonomically driven purchase suggestions. Adopting the 5S redesign should allow for further opportunities to improve and enhance the working space, making it increasingly lucrative for CVS while fostering a safe environment for its employees.
References
Chapman, C. D. (2005). Clean house with lean 5S. Quality Progress, 38(6), 27-32. Retrieved from Link
Lehto, M. R., & Landry, S. J. (2013). Introduction to human factors and ergonomics for engineers. Boca Raton, Flor.: CRC.
Middlesworth, AuthorMark. “A Step-by-Step Guide to the RULA Assessment Tool.”Ergonomics Plus, 7 Nov. 2017, Link