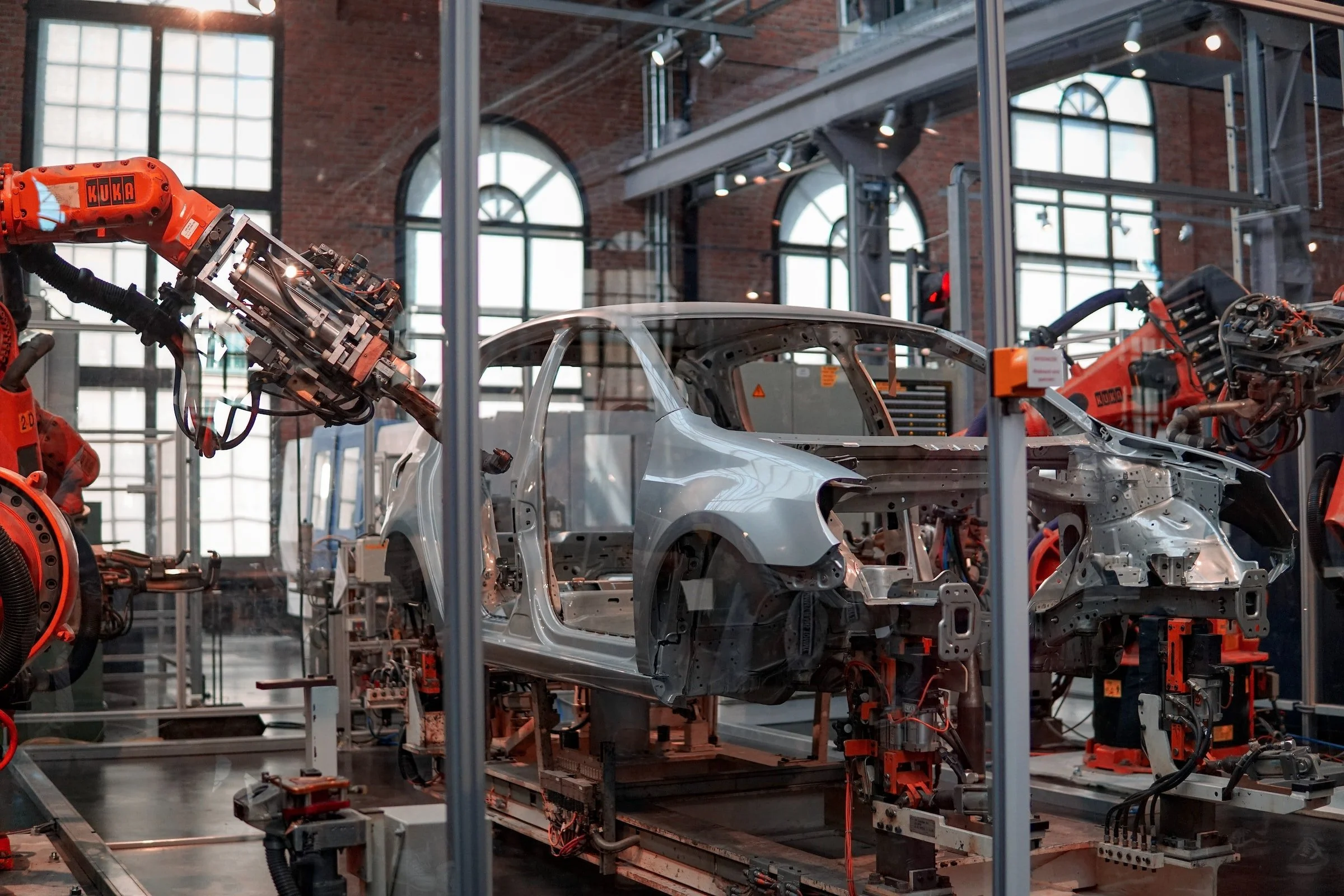
Deloitte.
Manufacturing 4.0
Digitizing Automotive Manufacturing through IoT
Deloitte was contracted to deliver on 10 Industry 4.0 use cases. The effort involved discovery, to identify the best-fit use cases, followed by designing custom applications and deploying them on an IoT platform and hardware assets
Limited data shared to protect client and firm IP
Digital Zone Board
All operations at the automotive manufacturer’s factory were dictated by a production system that was defined in the late 1990s. To keep activities in check, the operators were expected to follow guidelines provided on a ‘Zone Board’ that was specific to each manufacturing zone.
Our goal was to create a standard and scalable Digital Zone Board (DZB) on the IoT platform that would replace physical boards across the client’s global plants. The project we undertook was considered a pilot that had to act as a proof of concept to enable automatic data feeds and electronic forms for user input to enable faster decision-making and problem-solving. We built an intuitive, high-level view of each zone’s health to enable real-time response to data. This allowed users to view more detailed views of each production system activity and analyze trends.
Discovery
During the discovery process, the team identified several pain points. Interviewing operators, we found that they found it extremely time-consuming to keep up with the manual process. Zone managers reported inaccurate reporting and incomplete boards as a common occurrence. Most importantly, we identified potential in studying the historic data to identify trends - something that was currently not possible due to the manual process.
Shown alongside is the manual zone board that was being used as a global standard by the client. The production system board was designed as a workflow matrix where most ‘tiles’ fell under four vertical categories: Input, Process, Output, and Andon; and three horizontal categories: Safety, Quality, Flow
Design
The design process involved breaking down the matrix tiles and uncovering their most critical functionality before translating them to a digital medium. It was also critical to consider how data could be architectured to be input through the digital board and fed into the IoT platform’s data lake.
Given that this was a pilot program for an international overhaul of the production system, the client want to make incremental changes to the user interface. As such some of the visuals were made to mimic the physical board and much of the emphasis was on capturing real-time data and reporting smart analytics.
The design phase required our team to work closely with the client’s IT organization, partner with their developers overseas, and report to the business and manufacturing heads that were the sponsors and product owners/recipients of the deliverable. Prototypes were designed iteratively after discussing business goals and shipped to the development team to work on. Figure 1.1 shows an early sample of the analytics reporting tile based on the manufacturing team’s input.
Given that the team followed an agile software build process, the skeleton of the DZB came together iteratively. Plant operators were often invited to test digital tiles as they came together as a part of our user-centric design process. Fig 1.2 shows a minimal viable product of the work in progress DZB. Figures 1.3 provides the double click-view of a tile that managers could access to make staffing decisions based on skills data.
Figure 1.2
Figure 1.1
Figure 1.3
Deployment
Through an interactive design process, our team achieved buy-in from the business sponsors and the plant leads.
Our application was deployed on a heavy-duty touchscreen device that was connected to the IoT platform for data transmission.
Figures 2.1 and 2.2 showcase the deployed product being used by manufacturing operators. The pilot program won the trust of the client’s regional heads and approval was received to replicate the effort across 5 additional sites for a total of 60 digital zone boards. The replication effort was led by the client’s IT team
Figure 2.1
Figure 2.2
Disclaimer: All data shared on this page is considered the property of Deloitte Consulting LLP and the client. The author does not claim rights to any information and has only provided the same for an academic evaluation